Put to the Ultimate Test – Part 5: Fire Tests
During the development of our cables and wires, we vigorously test each product in our testing laboratories. In the fifth part of our series, we’ll introduce you to our fire tests.
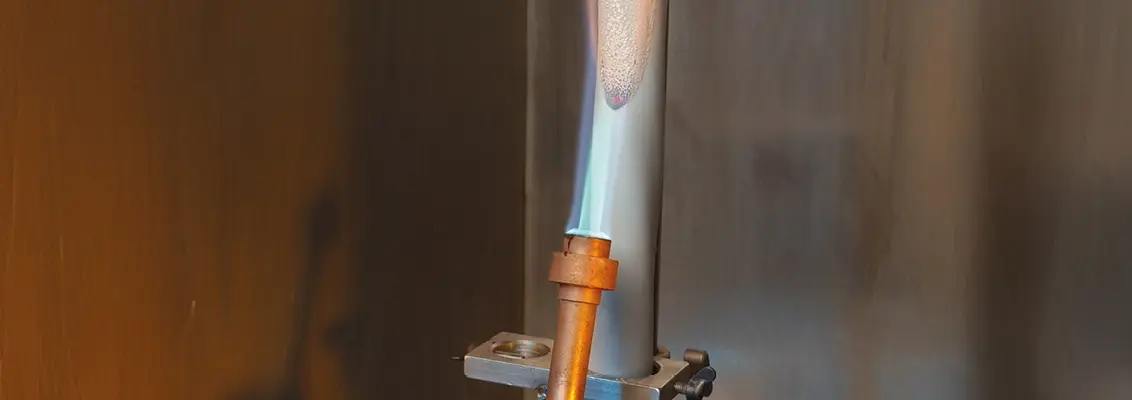
In both industrial applications as well as in building installations, fire prevention is of central importance. In many cases, fire can endanger lives or severely damage machines, plants, and infrastructure. Different standards and regulations such as UL, VDE, or ISO lay out specific requirements for how cables and wires should behave when subjected to fire. Depending on where they are being used, they must be flame resistant, non-propagating, and not emit toxic gases when burned.
To ensure that our products meet all required safety standards, we perform comprehensive fire tests in our testing laboratories. Cables are fixed either horizontally or vertically then exposed to the flame of a Bunsen burner. The exact procedure, as well as the strength and exposure time of the burner, differ according to the standard being tested for. When testing, technicians pay close attention to how quickly the flame propagates along the length of the cable and whether liquid plastic droplets form, which could cause the fire to spread.
Our engineers are only satisfied when the provisions laid out by the respective testing organisation are thoroughly fulfilled. Should a product require further tests, such as a bundle fire test or a smoke density test, we also perform these in cooperation with external institutions. This ensures that our cables and wires comply with all current fire prevention requirements and provide the maximum protection for people and materials.
Ask the Expert
How are cables and wires made to be flame retardant?
The most important factor for flame retardancy is the sheath material. The cable's outer sheath is, after all, always the first to come into contact with and react to fire. Some plastics that we utilise as sheath material, such as PVC, are inherently flame retardant. Others achieve this through the addition of flame retardants that contain halogens or minerals.
Why aren't all cables equally flame retardant?
Because, for example, mixing in flame retardants can negatively affect other properties of the cable, such as the flexibility or the temperature resistance and tensile strength. Adding to this is the fact that halogen-free cables are being required in more and more applications, since halogens react aggressively to fire and can be hazardous. They can cause chemical burns in the respiratory tract and corrosion in machines and buildings. This is why it is important to closely consider each individual application to make sure we find the ideal solution that has the right properties and meets all applicable regulations.
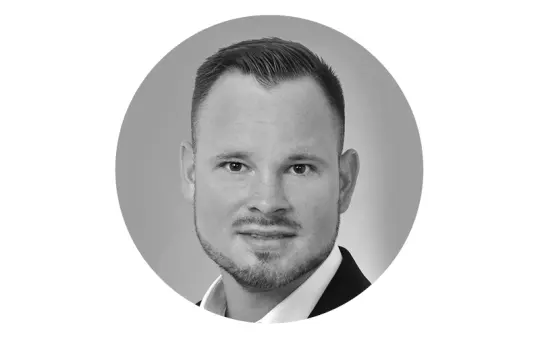