“Aluminium? Capricious, but manageable”
Aluminium instead of copper as a cable material is often a proven alternative in many cases. Thomas Blessing and Thomas Windisch from Carl Elektro-Anlagen (Carl Electromechanical Systems) discuss what to watch out for and what application opportunities there are with HELUKABEL expert Uwe Schenk.
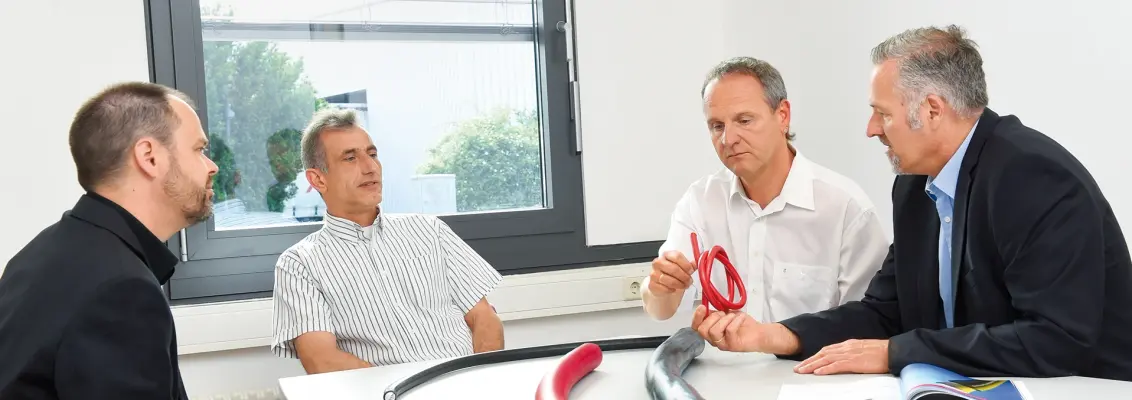
Gentlemen, why are we talking about aluminium as a cable material at all?
Thomas Blessing: Aluminium cables are often used to reduce cost and weight when compared to copper – including in our core business area, with turbines, transformers and UPS systems, i.e. systems for uninterrupted power supply. Aluminium weighs about half as much as copper, and costs one-third of the price. Additionally, while the price of aluminium remains relatively constant, the cost of copper fluctuates massively, and makes a safe calculation difficult. We therefore continue to make use of aluminium cables in our equipment and power supplies. |
Uwe Schenk: You’re in good company there. Aluminium has been an established material in long-distance transmission lines and infrastructure cabling, is used in wind turbines, and is conquering new fields in the aircraft and automobile sectors in connection with lightweight construction. And you also use aluminium cables in transformer stations and UPS systems. |
Thomas Blessing: Yes, but only a few RFQs in our core business explicitly demand aluminium cables. This is simply due to the fact that hardly anyone is interested in how energy arrives at the main distribution facility. If the customer is under cost pressure, an offer with aluminium cabling is always a variant, however. Some transformer manufacturers have also realized this recently. |
Thomas Windisch: When it comes to costs, many people only think of the cable price. But that’s a shortsighted viewpoint. Take, for example, the power cables installed throughout the ceilings of factories. If these were planned using aluminium cables, it would reduce the load by 40 to 50 percent. The supporting structure could then be designed to be simpler, and therefore cheaper. |
Thomas Blessing: Less weight is also an advantage for the installer. One metre (3 feet) of copper cable weighs around three kilograms (7 pounds), so halving the weight would be great. For example, when the installer has to lay cables for us in areas with raised floors. |
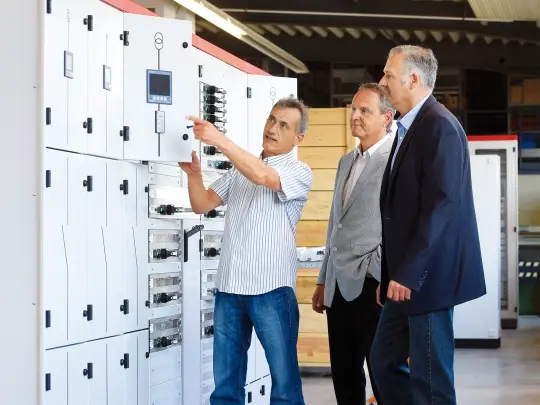
Copper or aluminium cable – what will end up in this distribution cabinet? Thomas Windisch and Thomas Blessing with Uwe Schenk (from left to right) in the manufacturing department of Carl Elektro-Anlagen. (© HELUKABEL / KD Busch)
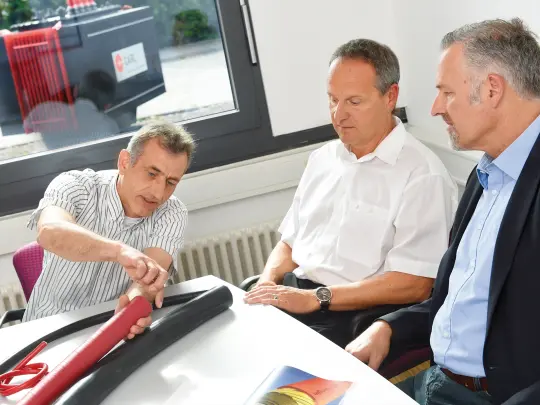
The editors in conversation with Thomas Windisch, Thomas Blessing and Uwe Schenk (left to right). (© HELUKABEL / KD Busch)
But let’s look at it away from the sunny side. What disadvantages does aluminium have?
Thomas Windisch: The electrical conductivity of aluminium is 35 percent lower than that of copper by volume. You therefore need larger cross sections for the same power transfer. Another shortcoming is that the surface of aluminium reacts very easily with oxygen, and forms a resistant oxide layer. Although this prevents further corrosion and makes the material extremely durable, it also reduces the conductivity and makes it difficult to make connections. |
Uwe Schenk: In addition, the socalled creep behaviour of aluminium must be taken into account. Under pressure, aluminium tends to elongate, which causes even the strongest of connections to lose their strength over time. Previously, aluminium cables were once contacted with simple, inadequate luster terminals. Completely inadequate. This led to an indelible impression of the long-term effects. |
Thomas Windisch: That’s not surprising, because if aluminium cables are connected improperly, things quickly become dicey. Particularly when in contact with nobler metals such as copper or brass. |
Uwe Schenk: That’s absolutely correct. An electrochemical reaction can occur, which can be triggered by condensation, for example. The current that follows causes aluminium to corrode, which can be seen as an expanding oxidation site, and results in high contact resistance. The fatal consequences are massive increases in temperature and sometimes even fire. |
Thomas Blessing: That’s right, but that doesn’t scare us. The material simply requires extreme care during processing. The installers have to be made aware of this, and be qualified to deal with these properties. In our experience, aluminium is capricious, but quite manageable. I also appreciate the fact that HELUKABEL expends a great deal of effort on certification, although this is not required by law to date. |
Lower conductivity, oxidation, inclination to elongate and demanding contact requirements – how do you deal with these into practice?
Thomas Windisch: The fact that a conductor made from aluminium requires a cross section around 67 percent bigger than a conductor made from copper can usually be taken into account in new designs, because the space requirement can be foreseen and planned for. We rely on proven components for the connection technology. |
Thomas Blessing: For example, we use bi-metal, Al/Cu cable lugs from HELUKABEL to make the contact between the aluminium and copper periphery. Because it’s fully enclosed, liquids canot penetrate, and creepage is negligible. I, for one, am convinced by HELUKABEL’s solution for connecting aluminium cables. |
Uwe Schenk: As already said, the oxide layer makes it difficult to make connections. It’s thereby necessary to break through it. This takes place initially by brushing the bare conductor ends before making the contact. Then during the crimp process, in conjunction with high compression, embedded corundum particles initiate a sandpaper effect that tears open the oxide layer of the aluminium. This allows a flawless electrical connection to be made. At the same time, the contact grease that was applied in the factory prevents moisture and oxygen from penetrating, thereby inhibiting any new corrosion. |
Thomas Windisch: I’m also a fan of compression connections. But the described approach only works on solid conductors. A solution that works for fine-wire conductor structures, such as those found in the POWERLINE ALU series, is needed. |
Uwe Schenk: In this case, due to the larger oxidised surface of the conductor, we would recommend the certified C8 crimping process. Its contours penetrate very deeply into the bundled strand, evenly tearing the surface of individual strands and thereby enabling optimal contact, even at the center of the bundle. With a filling level of 95 percent, the C8 crimp compensates for the elongation effect. |
Thomas Blessing: Within the procedures of our maintenance contracts, we have also placed the contact points on the check list for all systems. If the connections are OK, aluminium cabling is always a sure thing. |