Put to the Ultimate Test – Part 1: Torsion Tests
During the development of our cables and wires, we vigorously test each product in our testing laboratories. In the first part of our series, we’ll introduce you to torsion tests.
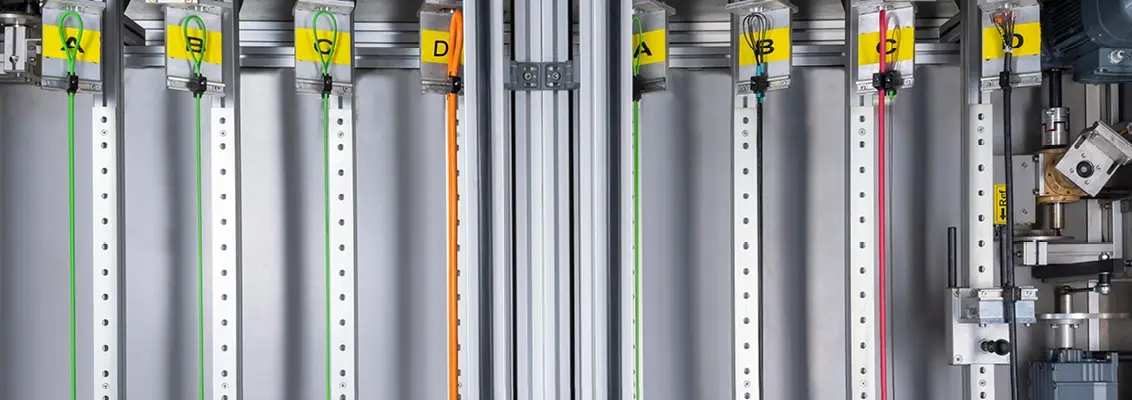
Cables and wires in industrial robots and other moving machine parts are often required to withstand extreme stresses caused by torsion. Constant repetitive movements put materials under considerable strain. At the same time, operators expect components to function perfectly and reliably throughout their entire service life to avoid disruptions, outages and safety hazards.
For this reason, at HELUKABEL, we simulate intensive and continuous torsion stresses under realistic conditions with our high-tech testing equipment in Windsbach, Franconia. We have several types of apparatus for doing this because some of our customers, for example those in the automotive industry, have very precise specifications for how a torsion test is carried out. The tests show that our cables and wires withstand speeds up to 1,000°/s, accelerations up to 2,000°/s² and torsion angles up to 720°. Hence, we make sure that each product always meets our customers’ high standards, and that they receive the impeccable quality they rightly expect from us as a leading supplier of cables, wires and accessories for more than 40 years.
What is torsion?
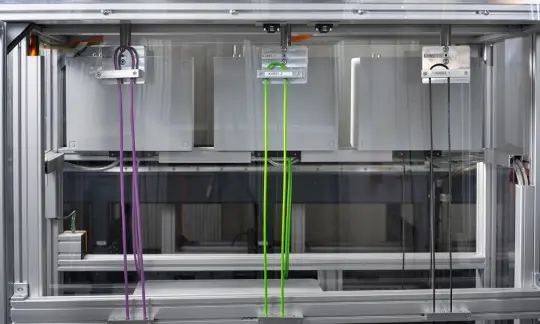
Torsion occurs when a cable is twisted along its longitudinal axis. This is often the case in robotic applications and in machinery and plant engineering, as well as in wind power plants. The resulting torque causes cable deformation. The phenomenon can be compared with wringing a wet towel. The wire is stretched at places and crushed at others, and these applied forces are constantly changing. The torsional strain increases linearly from the centre of the cable to the surface of the jacket where deformation and stress are at their greatest. To ensure that cables and wires are resistant to torsion, they require a special construction with the use of suitable materials.
Ask the expert
Mr Meyer, how do the impacts of torsion manifest themselves over time?
Continuous torsion significantly accelerates the ageing of cables and wires. For example, the outer sleeve deteriorates more quickly, and this is more pronounced when cheap rubber sleeves are used as opposed to sleeves made from high quality materials such as modified PVC or PUR. There are also diverse forces acting on the copper wires within the cable, which might cause them to break over time. The cable fixing points are also important: simple clips, for example, can’t easily allow torsional forces to pass through and are therefore subject to high shear forces. These are forces that are parallel to each other but in opposite directions, and that can cause a cable to break.
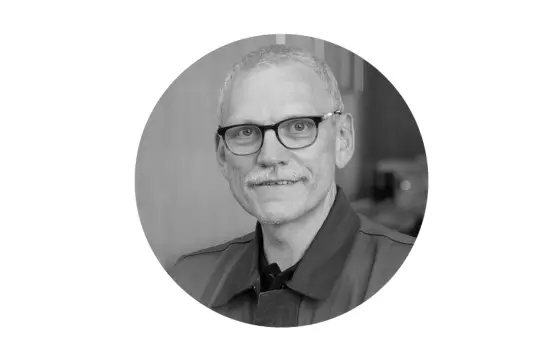
If shielded robotic cables are required for better electromagnetic compatibility (EMC), product developers choose a special shielding called the D-screen. What’s the difference between a C-screen and a D-screen?
A C-screen is a braid made of multiple copper wires laid alongside each other. It’s the most popular type of shielding in cable construction and is used, among other things, for drag chain cables. The C-screen is suitable for applications with bending stresses but not for ones with torsion. This is because it’s very difficult for the braid to return to its original state after being twisted along its longitudinal axis. This is why we use the so-called wrapped screen or D-screen for torsion-resistant cables. This type of copper wrapping is particularly flexible because there are no wires crossing over each other. The ability of the cable to allow torsional forces to pass through is improved and the cable can be twisted along its longitudinal axis without being damaged.